Find out how we work
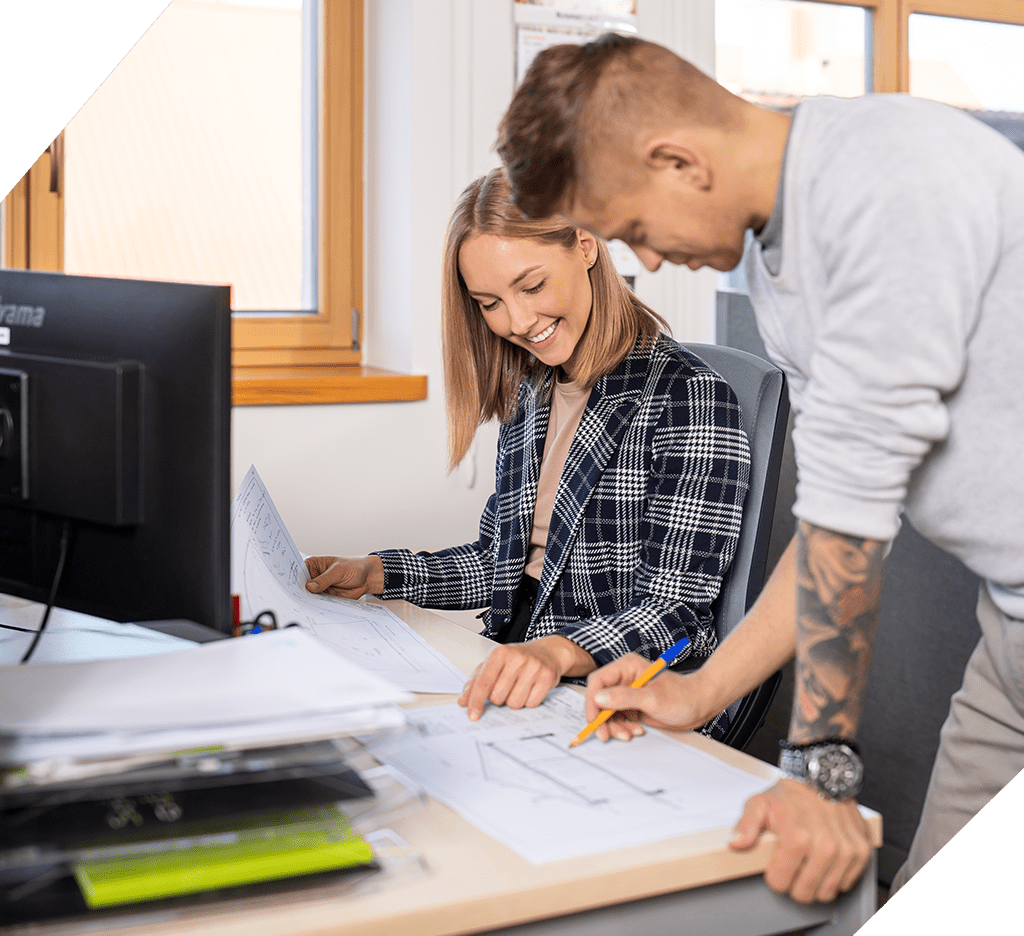
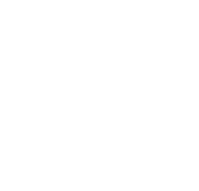
from the first
to the last step
Support/advisory service
From the first to the last step, the customer will be supported by contact person from our Customer Service Centre. This is the person responsible for ensuring that the cooperation runs smoothly and on time. Your contact person provides you with support and professional technical and commercial advice, and helps you to choose the best solution for your business customers, property developers and individual investors.
Design
How does the work of the design department look like? In the first stage, we prepare technical designs and workshop drawings. The support provided by modern technology in this regard is invaluable: Pamir computer software (supplied by the Mitek corporation), which we use to design trusses, and Dietrich’s 3D programme, developed for the design of carpentry and frame structures.
One of our main tasks is to provide professional advice and support in selecting the most optimal solutions for the customer. The calculation and drawing documentation created on this basis, as well as the 3D files, are sent to the customer in digital form. The technical design, signed by a certified constructor, is sent to the construction site together with the produced timber structure. It is the basis for professional and efficient assembly.
We take care of the high quality of our projects, which meet the needs of the investor and at the same time are in line with the values represented by the Burkietowicz Group: development, competence and partnership. Specialised tools combined with knowledge and competence, allow us to design “tailor-made” constructions that perfectly meet the needs of modern timber construction industry.
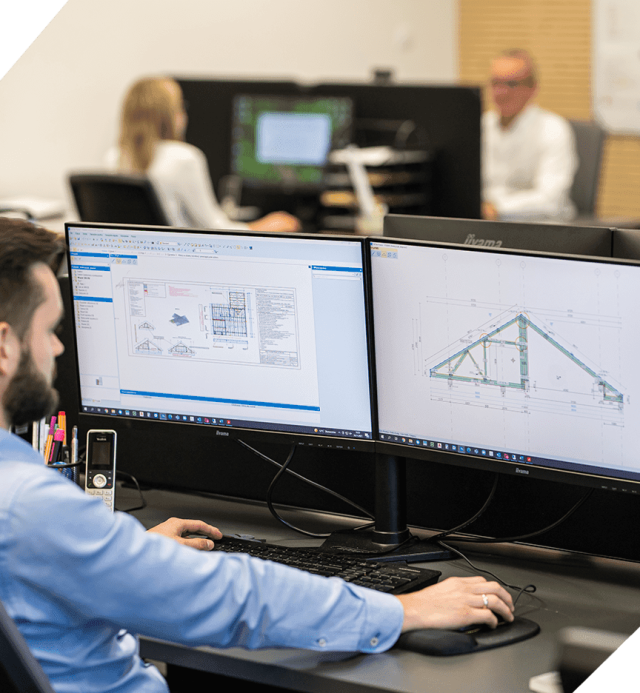
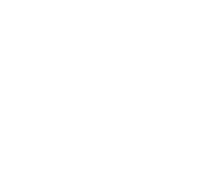
“TAILOR-MADE”
DESIGN
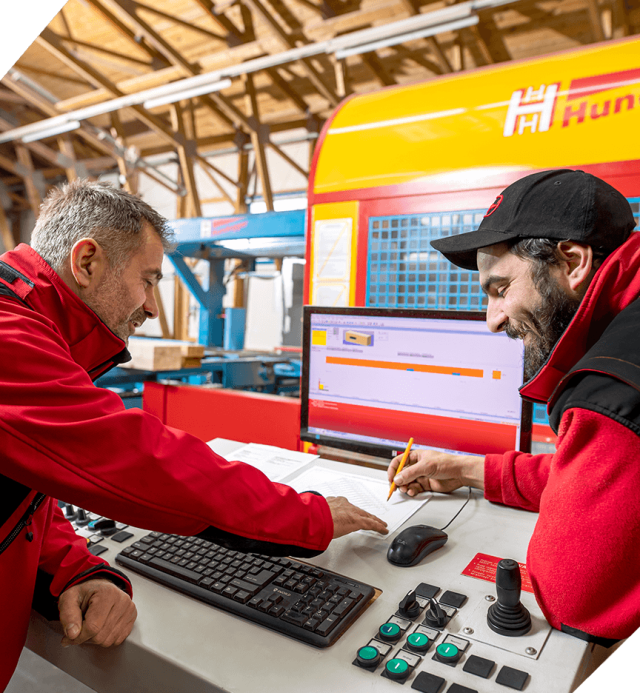
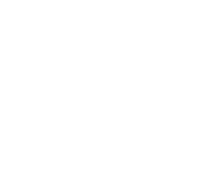
we know a lot about wood
and woodworking
production
Speed, precision, reduced costs – these are just a few examples of the benefits of prefabrication, i.e. the production of finished components off-site. Prefabricated elements require no additional processing – they are a finished product that, like blocks, are assembled into a complete unit on site.
How are our prefabricated elements made? The entire production process is fully mechanised. The Burkietowicz Group has one of the most modern round-wood sawing lines in Poland, with a capacity of up to 55,000m3 per year in a single-shift working system, which uses the advanced DWK technological line of the well-known German company EWD. Each log can be sawn according to an individual cut, according to a cutting list, or optimised on an ongoing basis for the highest material output for a given cut. The main material, sharp-edged boards, logs, square timber and beams are bundled after sawing. The side timber is fed into an automatic trimming machine, next sorted and bundled. More than 70% of the sawmill’s production goes into modern, computer-controlled kiln dryers. Boards and logs dried to the right moisture content are mainly used as a semi-finished product for the production of structural timber, which is graded using the machine method on a certified grading line. Our machine park also includes Hundegger numerical controlled (CNC) machines: a SpeedCut SC3 high-speed saw and a K2i joinery machine. Modern machines make the production process completely automatic, precise and fully repeatable. Eliminating the risk of mistakes, improving the machining of prefabricated parts to the maximum, as well as expert staff operating the machines guarantee the wide variety of offered services and allow us to respond flexibly to customers’ needs.
Our company conducts Factory Production Control based on EN 14081-1+A1 (structural timber production), PEN 15497:2014 (structural finger-jointed solid timber), EN 14080:2013 (glued solid timber), EN 14080:2013 (glued laminated timber) and PN-EN 14250:2011 (truss production). The finished product is CE marked, which allows it to be distributed in Poland and in the countries of the European Union.
transport
This means that our customers do not have to worry about the transport of prefabricated elements to the construction site – they can use the time saved to organise the subsequent stages of the project.
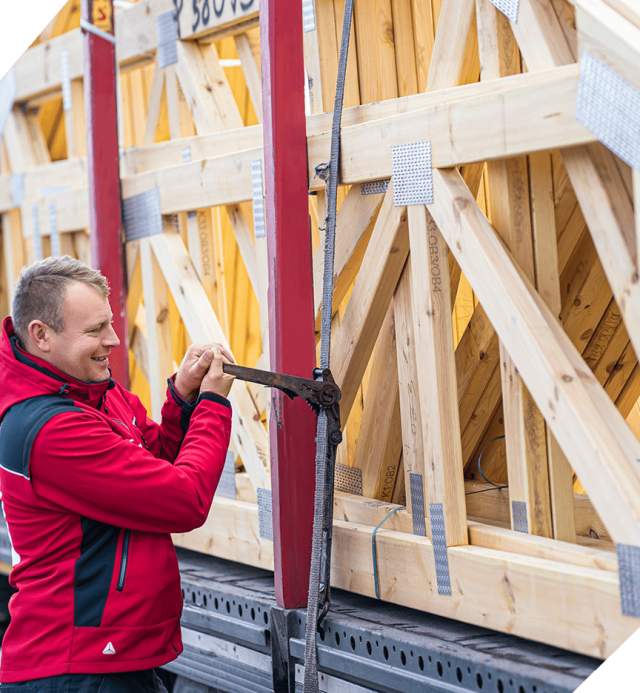
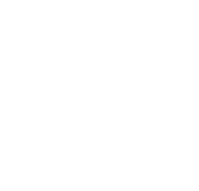
time is money
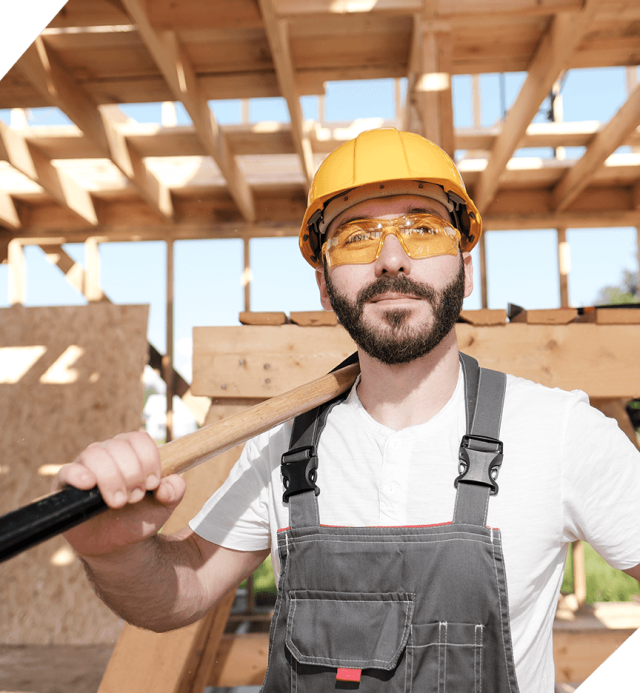
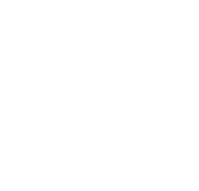
fast, economical
and safe
assembly
We place great importance on precise scheduling of work and support our partners in this regard. Efficiency, effectiveness and meeting the expectations of the customer/investor are key issues for us.